Project information
- Category: Other
- Client: Personal
- Project date: 2021
Project Objective
To improve CAD and 3D printing skills with Fusion 360 and the Ender 3 V2 printer
Overview
After recently purchasing a 3D printer, I needed to refresh my CAD skills since they had not been used since high school. There was also a need to fill up empty space in my apartment. 3D printed rockets are a great way to do this. Rockets can be simple in terms of modeling, as they have rotational symmetry, but they also provide a challenge in printing. This is because they are too big to print in one piece, so they must be broken into pieces and joints added to construct it back into one object. Fusion 360 is the tool of choice for this project, with it being free and having cloud saving.
Final Product
The Soyuz:
- 71 total parts, most of which are engines, and 17 unique parts
- 40 inches tall
- About 1 week print time
- 1053 grams (just over 1 roll) of polylactic acid (PLA) filament
- 17 total parts, and 15 unique parts
- 17 inches tall
- About 3 days print time
- 116 grams of PLA

Conclusion
This project successfully improved my CAD skills and taught me a lot about the capabilities of 3D printing, like joints. Joints can be very difficult, even at this large scale while trying to minimize filament usage and print times. Features of joints can be too small, meaning they will break easily. And super glue joints, while strong in this project, seeps through the PLA and bleaches it, ruining the look. This was the case with Electron as it was much smaller making strong glueless joints much more difficult. The Soyuz faired better as almost every connection outside of the engines (they were too small) used some sort of glueless joint. Friction joints also tend to wear away quickly with PLA and lose their effectiveness. Interlocking cylinders with an extruded tab sliding inside an L-shaped pathway ended up being the most successful joint that I tried.
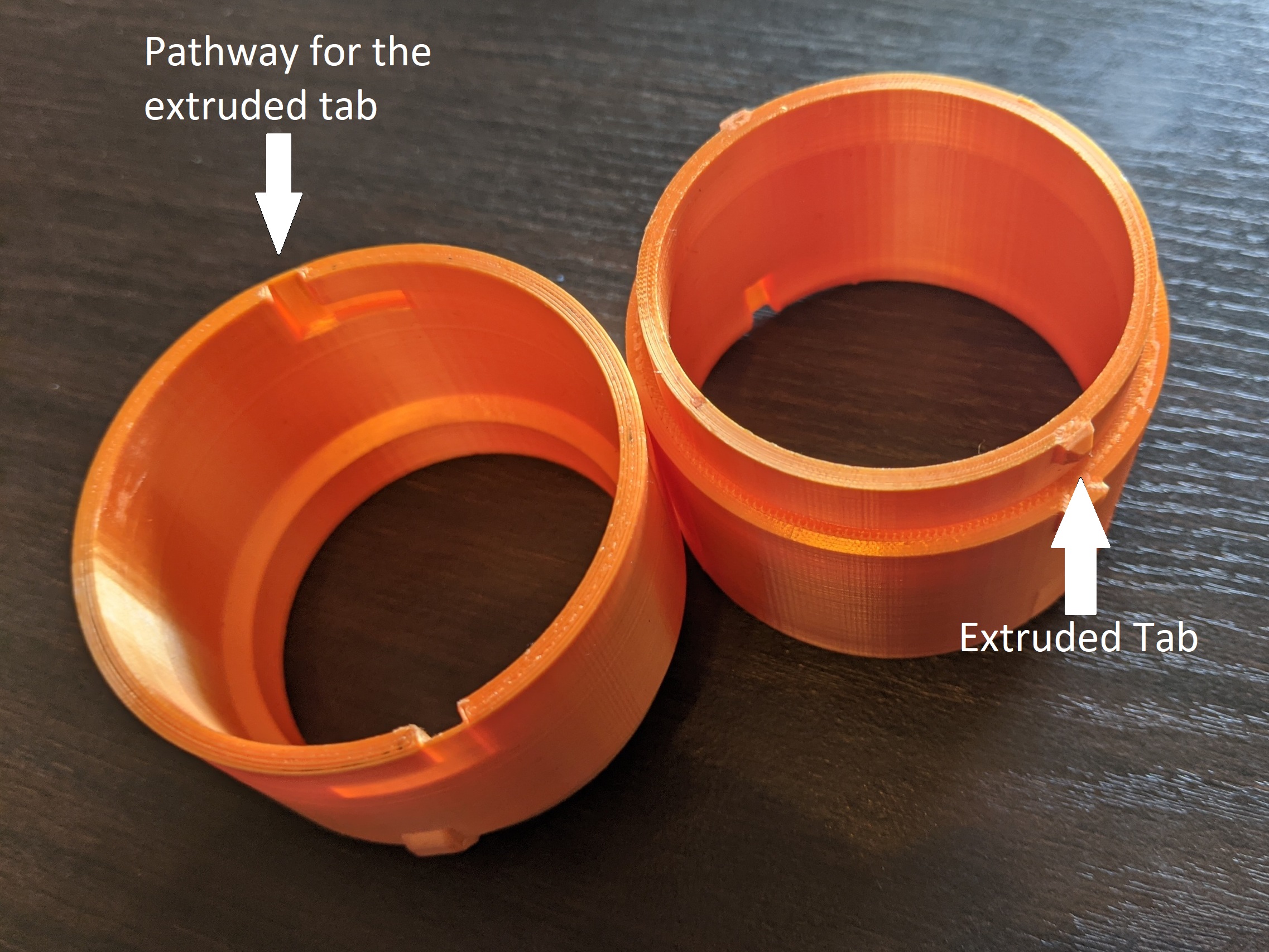